What is a GD&T Feature Control Frame?
A Feature Control Frame is a rectangular box that provides all the necessary information about the tolerance for a particular feature on a part. It consists of several compartments containing symbols and numbers that communicate tolerances in a structured, universally understood way.
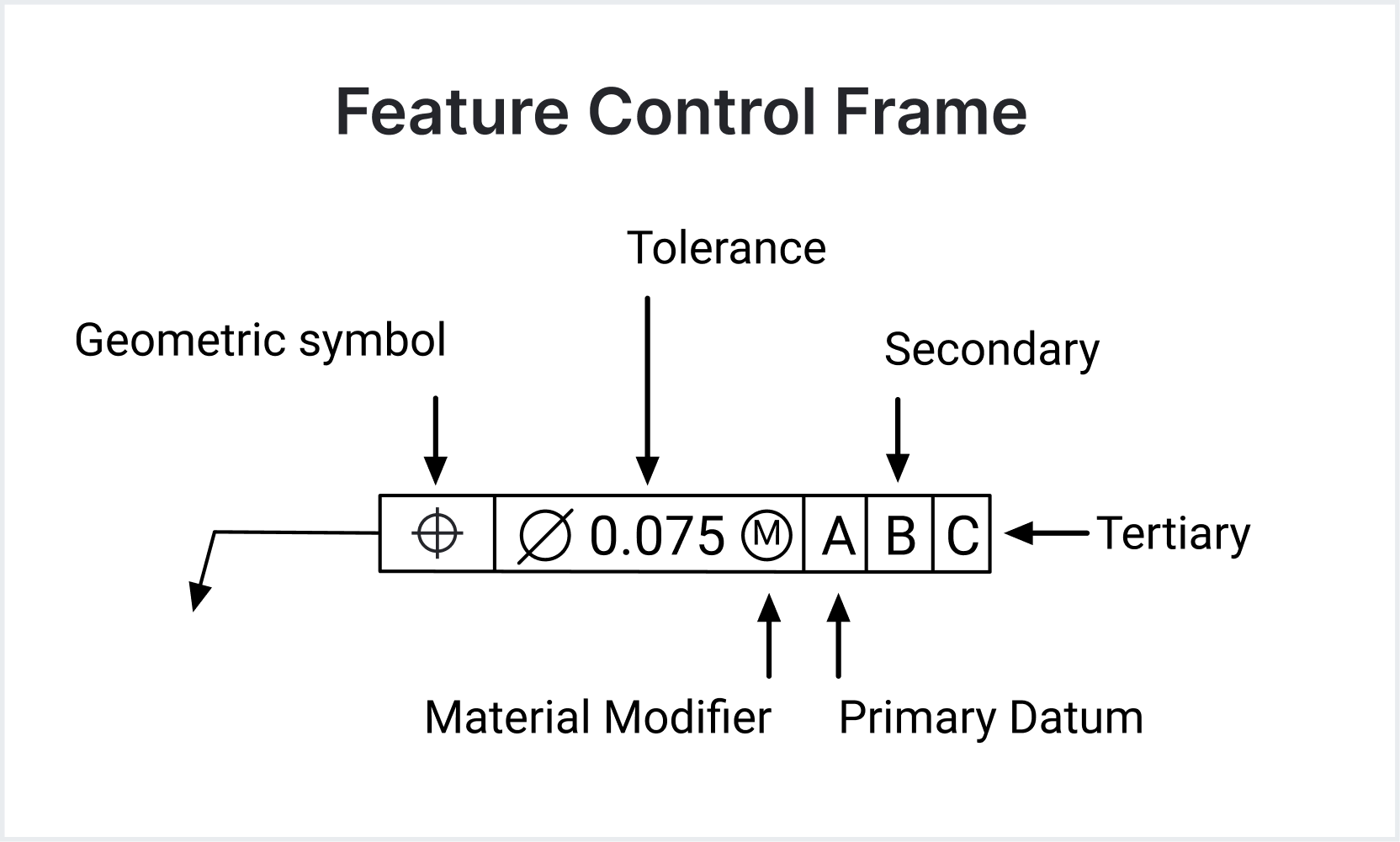
Anatomy of a Feature Control Frame
A typical feature control frame contains the following elements:
- Geometric Characteristic Symbol: This defines what kind of control you’re applying, such as flatness, perpendicularity, or position. It’s always the first thing you’ll see in the box.
- Tolerance Value: The next section specifies the tolerance allowed for the geometric characteristic. This number indicates the range of acceptability on the zone of tolerance and is in either metric or imperial units.
- Modifiers: These include conditions like Maximum Material Condition (MMC) or Least Material Condition (LMC). These material conditions allow you to specify the tolerance based on the part and feature’s size limits.
- Datum Reference Frame: These establish a coordinate system to measure the feature against. This indicates the constraints of how the Degrees of Freedom are controlled for each feature control frame measurement.
For example, if you’re controlling the position of a hole, your feature control frame will include a position symbol, the tolerance for its location, and datum references indicating how to measure that location.
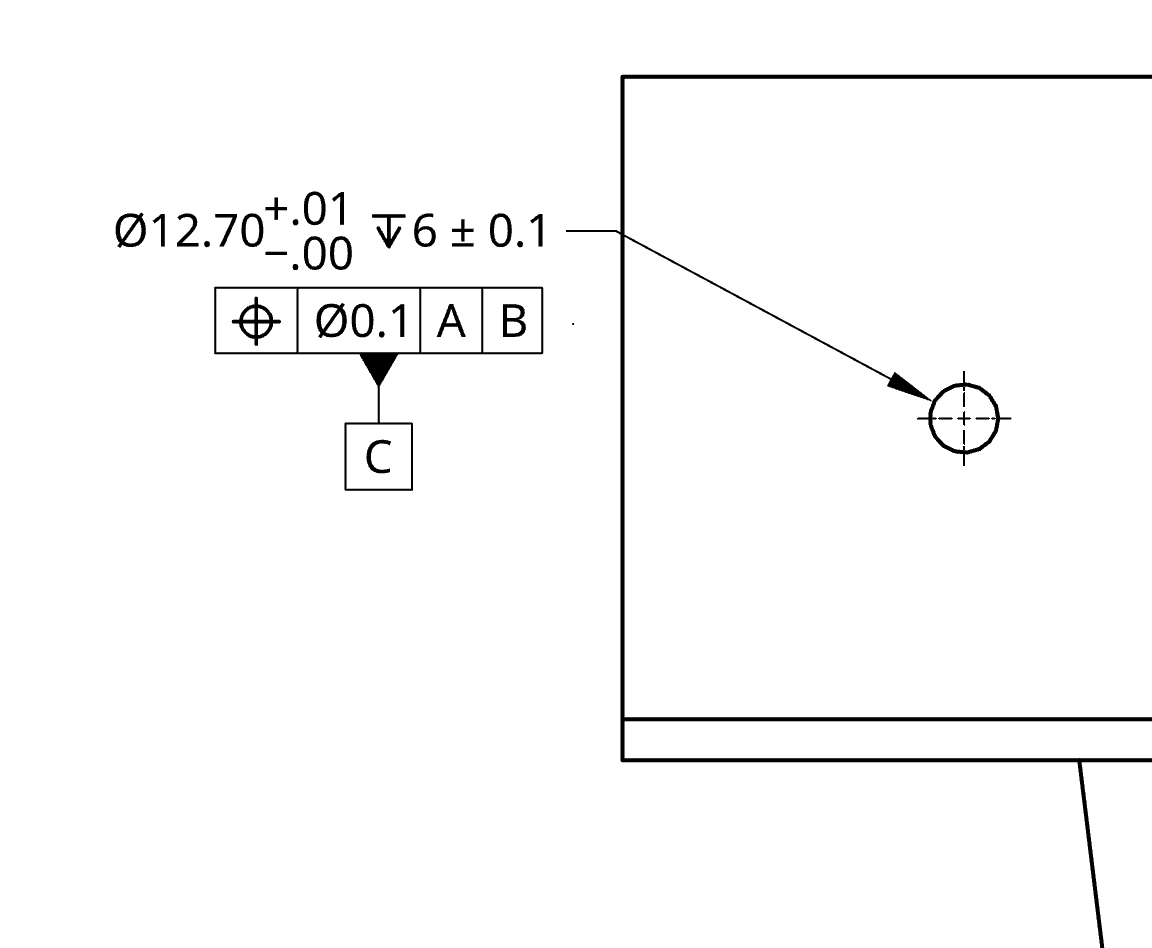
Why is the Feature Control Frame Important?
The Feature Control Frame is more than just a convenient notation system—it ensures that every part is produced and inspected to meet the required performance. It standardizes how tolerances are applied and understood across different teams, from design engineers to machinists and quality inspectors. Without this clarity, parts could be made inaccurately, leading to costly rework, assembly issues, or even product failure.
The Role of Datums
Datums play a critical role in many feature control frames. They serve as a point, line, or plane from which measurements are taken. When used correctly, datum references ensure that parts are oriented and located properly in an assembly, preventing misalignment.
For example, in a part with multiple holes, you might want each hole’s position to be relative to a central datum feature. This ensures that during assembly, all the holes align as intended.
Applying Feature Control Frames in Engineering Drawings
When adding a feature control frame to your drawing, follow these best practices to ensure clarity and manufacturability:
- Choose the Correct Geometric Characteristic Symbol: Before placing a feature control frame, determine what type of control is required for the feature. Is it essential that a surface is flat? Should a hole be centered precisely? What should a feature be controlled against to meet the functional requirements? The characteristic symbol you choose directly impacts the part’s function and how it will be inspected.
- Select an Appropriate Tolerance: The tolerance value dictates how much deviation from the ideal geometry is acceptable. Too tight, and you risk driving up manufacturing costs. Too loose, and the part may not function as intended. Striking the right balance between manufacturability and function is key.
- Include Datum References (When Necessary): In some cases, controlling a feature requires more than just an absolute tolerance—you need to control how the feature interacts with others. For these situations, include datum references in your feature control frame. Make sure your datum system is logical and based on how the part will be used or assembled.
Example of a Feature Control Frame
Let’s consider the case of a hole in a bracket that needs to be precisely positioned relative to the edges of the bracket.
The feature control frame might look something like this:
- The first box contains the position symbol (⌖).
- The second box contains the tolerance value, say 0.005 in.
- The next three boxes represent datum references (A, B, and C), indicating the part’s edges from which the hole’s location is measured.
This tells the machinist that the hole must be within a 0.1 mm tolerance zone from the ideal location, as measured relative to the datums A, B, and C.
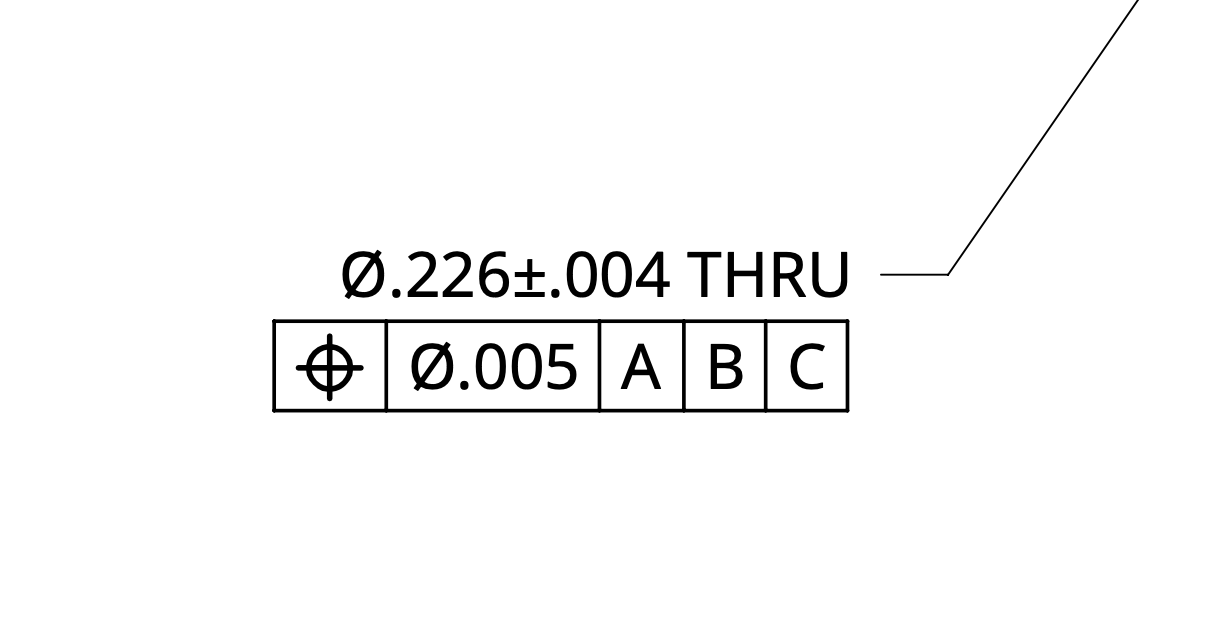
Practical Challenges and Tips for Using Feature Control Frames
1. Overly Tight Tolerances
A common mistake is specifying overly tight tolerances in feature control frames, which can lead to higher manufacturing costs or parts that are difficult to produce. Always consider the capability of your manufacturing process and how critical the tolerance is to the part’s function.
2. Poor Datum Selection
Another challenge is improper datum selection. If your datums don’t reflect the true assembly conditions, you may end up with parts that are technically within tolerance but don’t fit together in the final product. Think about how the part will be used and inspected when selecting datums.
3. Communicating Tolerances Across Teams
Make sure all stakeholders understand the importance of the tolerances specified in feature control frames. Regular communication between designers, manufacturers, and inspectors ensures that the tolerances are achievable and the parts meet functional requirements.
Feature Control Frames for Precision Engineering
Feature control frames in GD&T are essential for specifying and controlling part features to ensure functionality and manufacturability. By clearly communicating the required geometric characteristics, tolerances, and datum references, these frames ensure that your parts will fit together and function as intended, reducing costly errors and improving efficiency.
Mastering the use of feature control frames is a critical skill for any engineer working in precision industries. Remember to always choose the correct characteristic symbol, set appropriate tolerances, and use logical datums. By doing so, you’ll set your project up for success from design through to final production.