What Are Basic Dimensions?
A basic dimension is a theoretically exact value used to define the size, shape, orientation, or location of a feature. Unlike other dimensions, basic dimensions are not subject to manufacturing tolerances themselves; instead, they are used in conjunction with GD&T controls (such as position, profile, or angularity) to specify the permissible variation of the feature.
For example, if a hole’s location is defined as 25.00mm from an edge with a position tolerance of Ø0.1, the 25.00mm is the basic dimension, while the Ø0.1 defines how much deviation is allowed in the hole’s actual location.
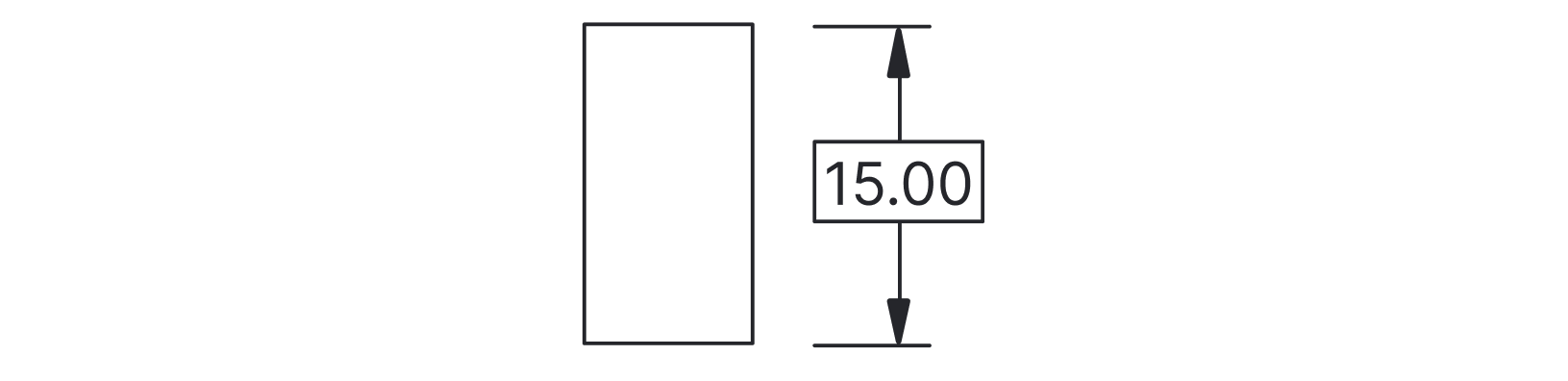
Key Characteristics of Basic Dimensions
- Theoretically Exact: A basic dimension provides an unambiguous reference for the geometry without considering manufacturing imperfections.
- Boxed for Clarity: On drawings, basic dimensions are enclosed in rectangular boxes to distinguish them from other dimensions.
- Linked to GD&T Features: Basic dimensions work in tandem with feature control frames, datums, and tolerance zones to ensure functional relationships between parts.
- Not Directly Toleranced: Basic dimensions rely on associated GD&T controls to define permissible variations. Anytime you see a basic dimension you know the surface or feature is controlled with a feature control frame. This reduces confusion and ambiguity.
Why Are Basic Dimensions Important?
- Simplified Communication: Basic dimensions clearly define design intent by focusing on ideal geometry, making it easier for designers, machinists, and inspectors to understand requirements.
- Consistency Across Teams: Since basic dimensions are exact, they eliminate the guesswork and ensure all stakeholders work toward the same geometrical targets.
- Alignment with GD&T Principles: They provide the reference framework necessary for defining tolerance zones, ensuring the functionality of assemblies.
How Are Basic Dimensions Used?
Locating Features :Basic dimensions are commonly used to locate features relative to datums. For example, the center of a hole might be defined as being 12mm from one edge (datum A) and 12mm from another edge.
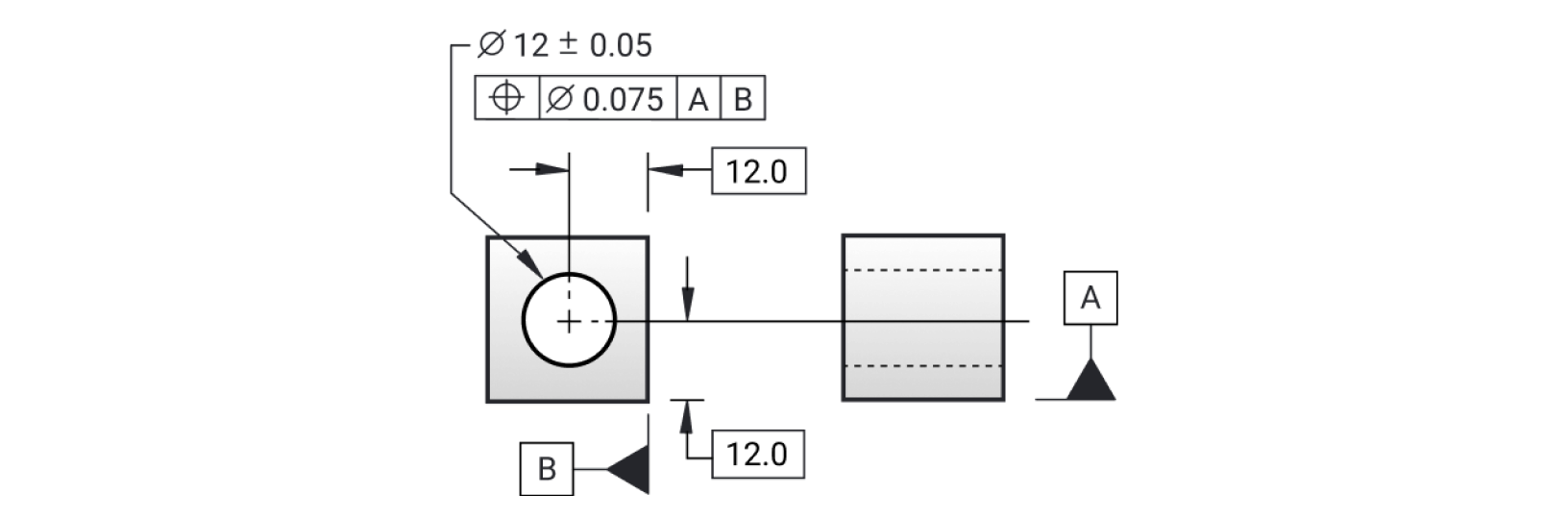
Defining Profile Geometry: For complex surfaces, basic dimensions define the ideal shape and size. A profile tolerance is then applied to allow for controlled deviation.
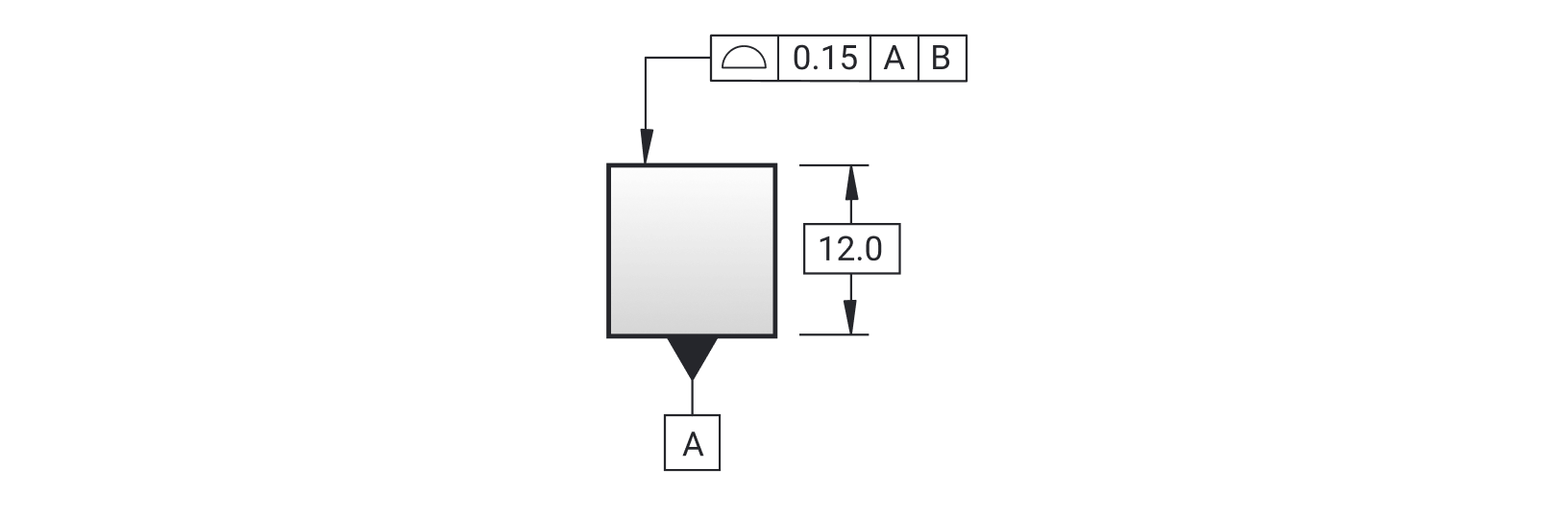
Specifying Angles: Angles between surfaces or features can be defined as basic dimensions, with angularity tolerances ensuring permissible variations.
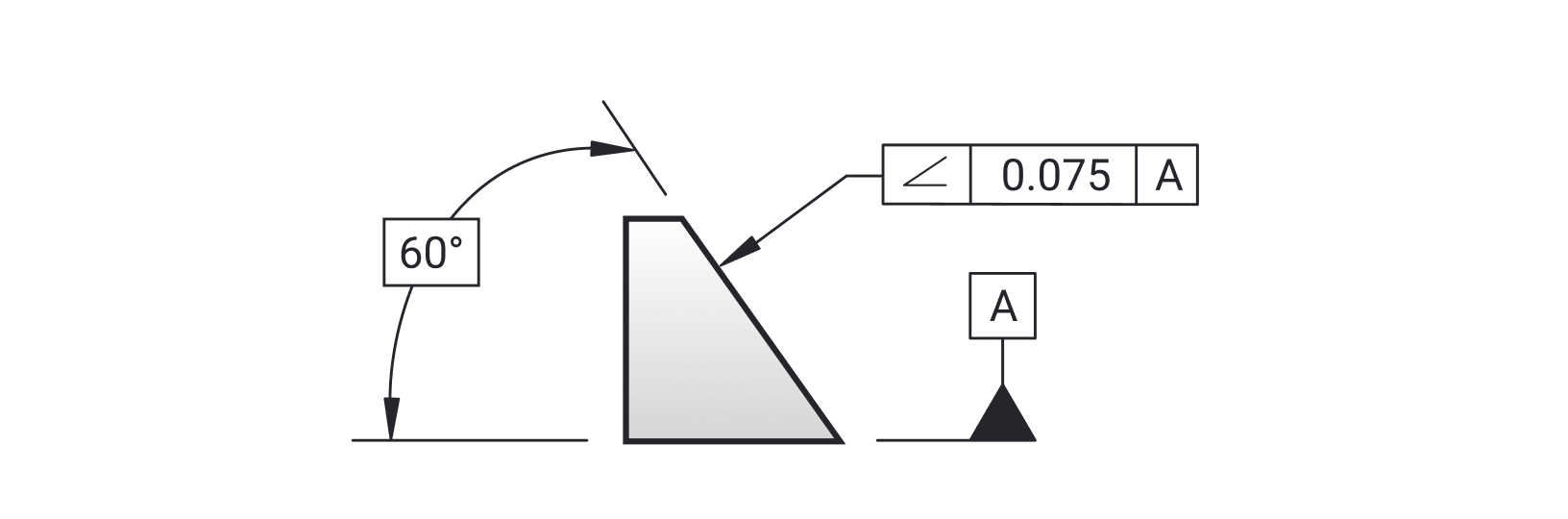
Example of Basic Dimensions in Practice
Consider a part with two holes that needs to align with a mating pin. The drawing might show:
- Hole size: Ø10.0 ±0.02
- Basic dimensions: 28.00mm and 32.00mm from datums A and B
- Position tolerance: Ø0.5 relative to A and B
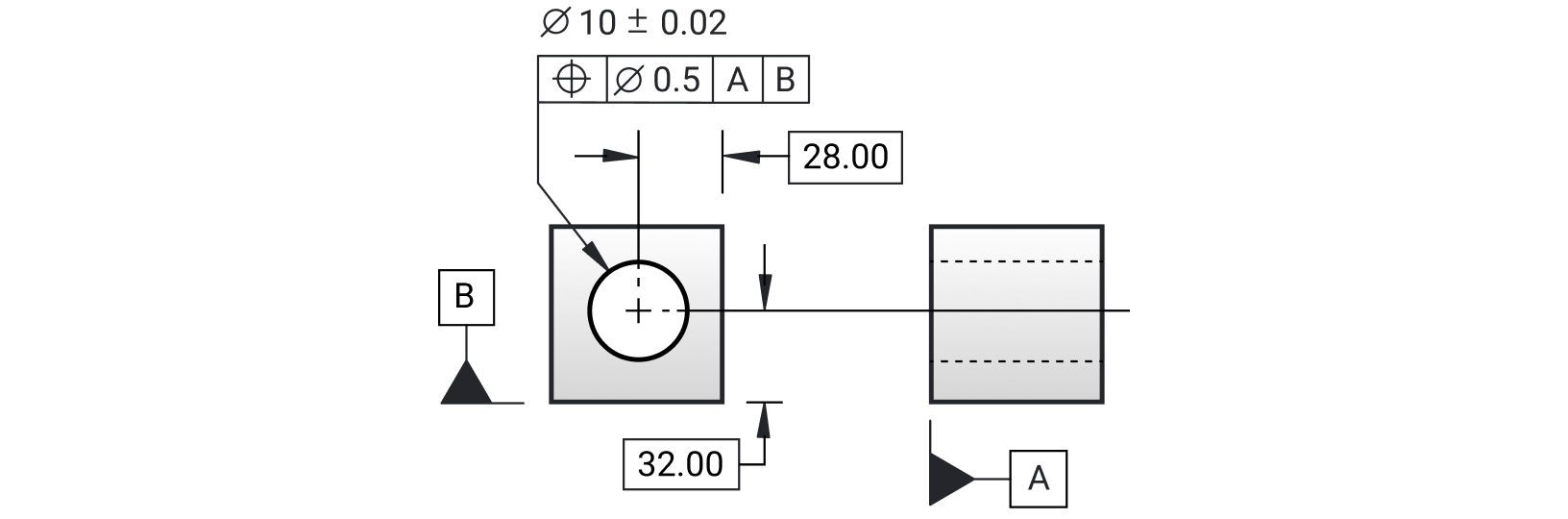
Here, the 28.00mm and 32.00mm are the exact, theoretical distances from the datums. The position tolerance specifies how much the actual hole centers can deviate while ensuring proper fit and function.
Inspection of Basic Dimensions
Since basic dimensions are theoretically exact, they are not directly measured or inspected. Instead, their associated GD&T tolerances (e.g., position, profile) are inspected. Inspection tools such as Coordinate Measuring Machines (CMMs) and functional gages are used to verify that the feature lies within its tolerance zone, as defined by the basic dimensions and GD&T controls.
For example, when verifying the location of a hole, the CMM checks the center’s actual position relative to the datums and compares it to the basic dimensions and positional tolerance.
Tips for Using Basic Dimensions
- Avoid over-dimensioning: Let GD&T tolerances do the work of defining permissible variation, keeping basic dimensions clear and simple.
- Choose Reliable Datums: Ensure the datums referenced by basic dimensions accurately reflect the part’s functional requirements.
- Communicate with Inspectors: Collaborate with quality teams to ensure inspection methods align with basic dimensions and GD&T controls.
Common Misconceptions About Basic Dimensions
- They Are Toleranced: Basic dimensions are exact by definition. Tolerances come from the associated GD&T feature control frames, not the dimension itself.
- They Apply Only to Simple Features: Basic dimensions can describe anything from hole locations to complex curved surfaces.
- They Are Optional: In GD&T, basic dimensions are a fundamental part of defining features, especially when tolerances are involved.
Basic dimensions are a cornerstone of GD&T, providing the theoretical framework needed to define precise geometry in mechanical designs. By understanding how to apply and interpret basic dimensions effectively, engineers can create drawings that minimize ambiguity, improve manufacturability, and ensure consistent quality. Whether you’re designing simple parts or complex assemblies, mastering basic dimensions will elevate your engineering practice.
If you have questions about basic dimensions or GD&T, feel free to reach out. We’re here to help you bring your designs to life with clarity and precision!